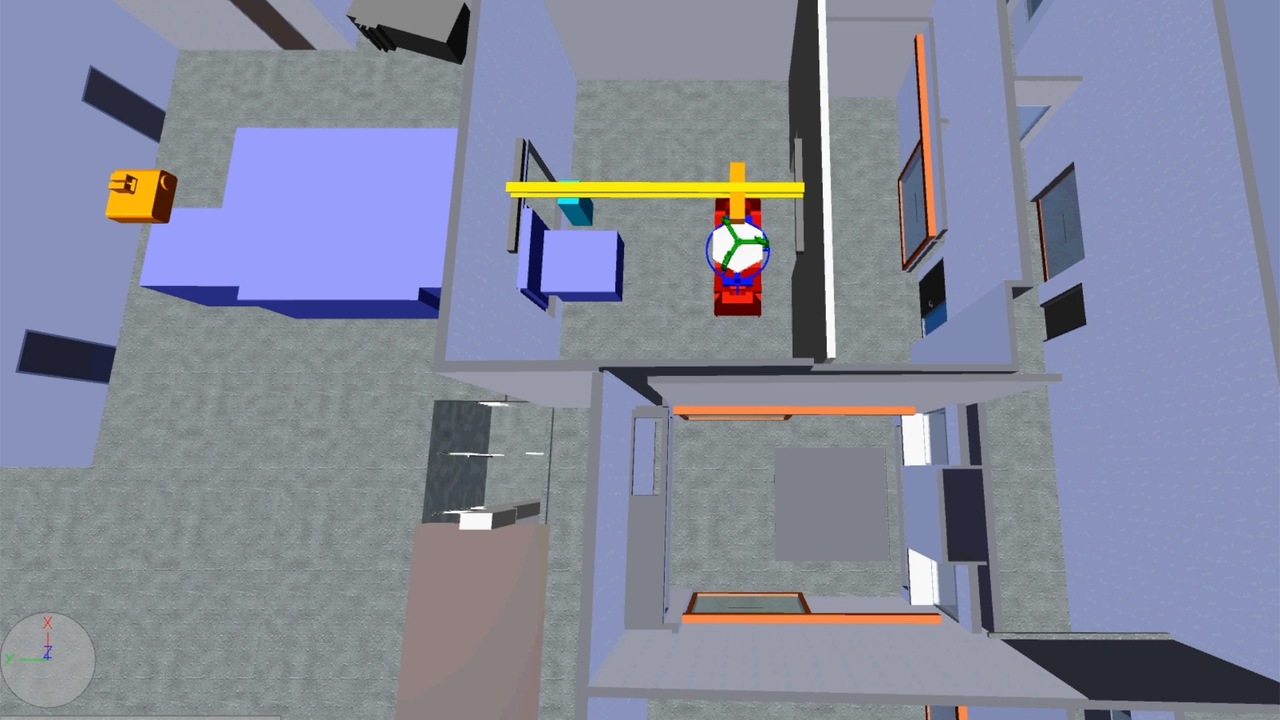
Snapshot of TMT’s mirror segment handling system - A TMT segment assembly is fastened onto the segment handling cart for safe transport within the observatory summit facility - Image credit: TMT International Observatory
Snapshot of TMT’s mirror segment handling system - A TMT segment assembly is fastened onto the segment handling cart for safe transport within the observatory summit facility - Image credit: TMT International Observatory
Pasadena, CA – The handling equipment for TMT primary mirror (M1) segment recently passed its Preliminary Design Review. The custom-designed equipment and tooling will be used to safely handle mirrors within the observatory during operational activities.
The handling of TMT mirrors will require specific equipment and an extreme level of care. Mirror segment manipulation will be necessary during maintenance activities, as mirrors are brought to the observatory, installed at the telescope and periodically removed for maintenance, as well as stored when not in use. This review, which happened remotely due to Covid-19 travel restrictions, focused on evaluating the design of TMT’s segment handling cart and its exchange frames, as well as the segment storage cabinets, lifting jacks and general lifting fixtures.
To facilitate the visualization of the mirror handling activities and operational processes, the TMT’s System Engineering team prepared a set of animations representing the main use cases of the M1 segment handling equipment. These animations featured an overview of one TMT segment’s exchange, its transfer between the mirror coating areas, and its storage into cabinets at the observatory.
Josh Church, TMT Mechanical Systems Engineer, said: “Preserving the cutting-edge performance of these large mirrors requires a rigorous service and maintenance plan. TMT’s handling equipment will be critical for the safe, efficient transportation of these delicate glass-ceramic mirrors within the observatory.”
M1 Mirror Exchange preview
TMT segment exchange animation. A TMT segment is lifted out of its position from within the mirror cell and transported down to the observatory floor. A replacement spare segment is then transported into position to be lifted onto the handling tool. Video credit: TMT International Observatory
TMT engineers have designed the telescope’s Segment Handling System (SHS) for highly trained personnel to safely remove segments and install freshly re-coated optics into the mirror cell (animation #1). During this segment exchange process, the TMT summit crew will remove and replace ten of the 492 segments every two weeks in order to preserve the outstanding mirror reflectivity required to keep TMT at the cutting edge of astronomical research.
To remove a segment from TMT’s 30-meter mirror structure, the telescope must be positioned vertically, so that the SHS, which is mounted onto the telescope structure, can be lowered, and its robotic hand can extract the segment using Vee-blocks.
The 230-kg segment and support assembly will be individually and carefully hoisted out from the telescope support structure and lowered to the observatory ground floor. Once securely fastened with clamps onto specially designed segment handling carts, the segments will be wheeled from the dome through the observatory corridor and into the mirror maintenance area, which includes the segment cleaning room and the mirror coating vacuum chamber.
TMT Segment Handling Cart Interface Model - TMT engineers designed customized wheeled carts that will be used for handling and transporting segments during segment exchange, maintenance, cleaning, stripping, coating and storage. Image credit: TMT International Observatory
During the meeting, TMT Engineers presented prototypes of the segment handling cart and lifting jack used at
TMT Segment Handling Cart Prototype and Activity at TMT’s technical lab in California - TMT handling cart prototype and segment lifting jack during segment testing at the TMT Integration & Test Facility. Image credit: TMT International Observatory
the TMT lab, where several tests have been successfully performed.
M1 Mirror Segment Recoating preview
TMT segment recoating animation - Sequences of TMT primary mirror segment recoating. The segment is transported to the maintenance and recoating chambers to receive a new pristine reflective coating - Video credit: TMT International Observatory
The mirror recoating process will require physically removing each individual segment assembly from the telescope structure. Once in the clean-room, optics maintenance personnel will carry out a visual inspection and verify that the glass is in great condition and the electronics are working properly. After the inspections are complete, the segment will be stripped of its old silver coat, carefully maneuvered onto the cart, and installed into the mirror coating chamber where a fresh layer of protected silver will be deposited on its surface.
The quality of the TMT mirror coating is one of the most critical aspects of telescope design. It is the material that collects incoming photons, which have sometimes travelled for billions of years throughout the cosmos, and reflects them towards the science instruments where they will be analyzed by TMT partnership astronomers. This sub-μm thick coating layer is an extremely delicate metallic assemblage that can lose its reflectivity over time due to exposure to air, dust and changing weather conditions. As a result, in addition to the individual re-coating process which will be carried out every two years, TMT personnel will regularly clean the mirror segments using a spray of carbon dioxide snow that will blow dust and grit from the surface through a process called sublimation.[1]
“We are thankful for the positive feedback from the review committee and will continue to invest a lot of effort in the design of the system handling equipment that will be essential for the maintenance operations,” said Alan Tubb, TMT Opto Mechanical Engineer. “The next steps will focus on pursuing the design in conjunction with that of the segment stripping and coating operations.”
Storage Cabinets preview for M1 Mirrors
TMT segment storage animation - Overview of one TMT mirror segment placed into a storage cabinet located in a dedicated and organized space on the observatory ground floor - Video credit: TMT International Observatory
In this last animation, the TMT cart is positioned under a monorail crane equipped with a segment lifting fixture. The crane is lowered down and used to raise the segment up and to transport it to the cabinets where a storage drawer has already been extended out. The segment is then lowered down onto the drawer and engaged to a central tube structure to secure it. These storage cabinets will be capable of housing the fully recoated 82 spare segments into a secured and protected environment until they are re-installed onto the M1 cell.
“The level of design of the segment handling equipment is much advanced for this preliminary stage,” said Eric Hansen, TMT Telescope Department Head. “Congratulations to the Optics, Telescope Controls & Structure, Safety/Quality Assurance and Systems Engineering groups for their tremendous teamwork and for providing an excellent level of design support from the very beginning of the project.”
Over the next months, the M1 handling equipment will continue to mature further the details of its design, taking into account operational concepts, system interfaces and technical requirements, while always keeping risks assessment and mitigating strategies at the forefront.
Screenshot of the TMT Mirror Segment Handling Equipment review participants on April 21, 2021 - Image credit: TMT International Observatory
Remembering Hugh Thompson
TMT Metrology Equipment Arrives in California