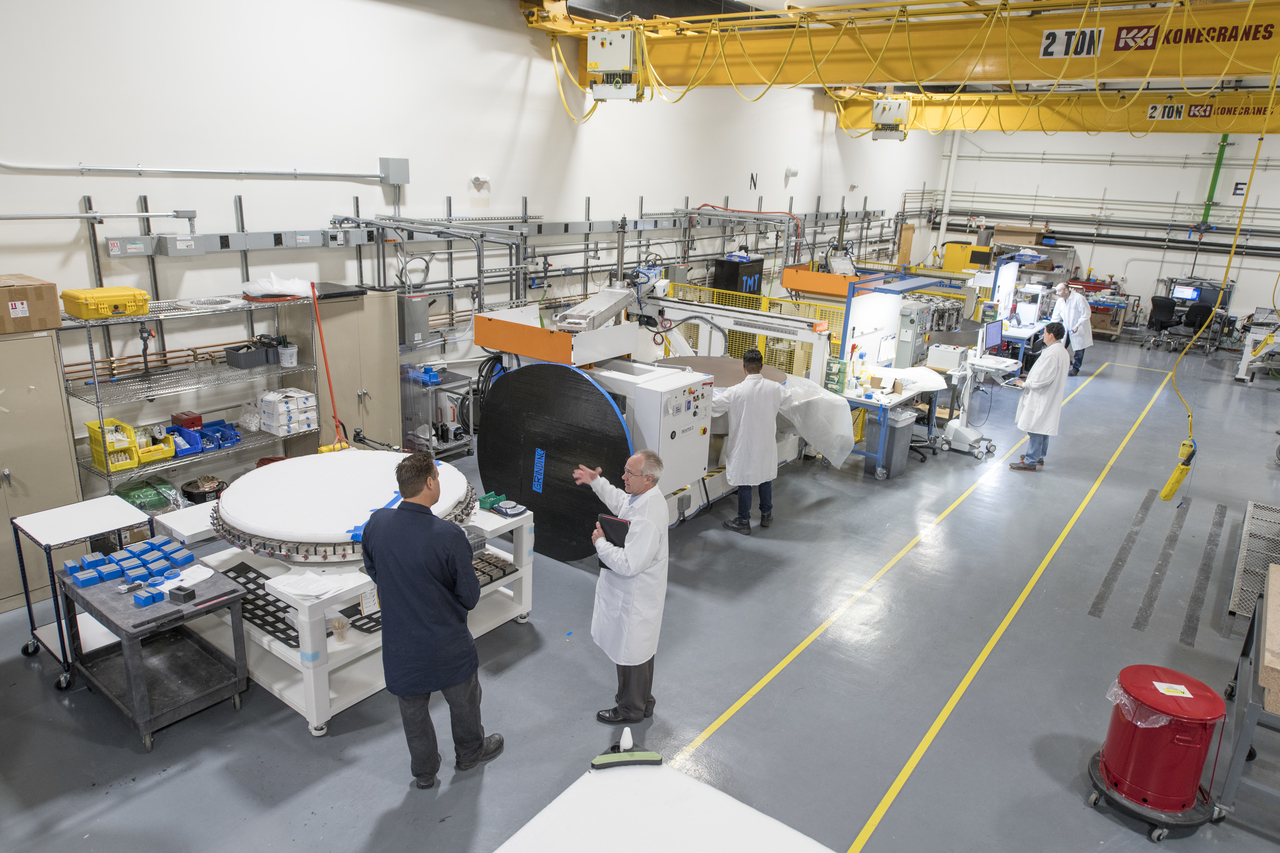
California-based Coherent, Inc. Production Facility - Coherent production facility dedicated to TMT Polishing and Hexing processes - Image credit: Coherent, Inc.
California-based Coherent, Inc. Production Facility - Coherent production facility dedicated to TMT Polishing and Hexing processes - Image credit: Coherent, Inc.
Pasadena, CA – A major milestone for the international Thirty Meter Telescope project (TMT) was reached in October 2020, as TMT selected California-based Coherent, Inc. for the Hexagonal cutting of the US allocation of its Primary Mirror (M1) segments. Coherent is one of the world’s leading providers of photonic solutions, including lasers and custom optics, and has extensive experience in large-scale precision optics and assemblies, such as those required for the TMT. Coherent was previously awarded the contract for polishing the US allocation of M1 segments.
TMT polished aspheric primary mirror segment being polished at Coherent production facility in California - Image credit: Coherent, Inc.
TMT polished aspheric primary mirror segment at Coherent production facility in California - Image credit: Coherent, Inc.
TMT and Coherent successfully held a virtual kick-off review for the next phase of TMT mirror segment manufacturing. After polishing the segments to a high accuracy, M1 segments will undergo a delicate fabrication process called Hex Cutting or “Hexing”. This is the critical process of cutting the 1.44m round, polished aspheric mirror segments (“roundels”) into their final hexagonal shape, enabling the close packing and precise positioning in the large M1 TMT primary mirror array.
TMT full-size Primary Mirror Segment Hexagonal cutting - Each TMT segment must be cut into a hexagonal shape and carved at critical dimensions for lodging high precision support components known as the central diaphragm and two edge sensors on each side - Image credit: Nanjing Institute of Astronomical Optics and Technology (NIAOT), National Astronomical Observatories.
The multi-step Hexing process involves a series of precision material removal operations, transforming a polished roundel into a hexagonal segment.
These processes include cutting the roundel outer perimeter and pocketing the back side of the mirror segment with sensor pockets and central diaphragm cavity. These features are used for bonding the glass segment with its mechanical support assembly.
Extremely precise and specialized equipment is required to meet strict TMT technical requirements. For that reason, Coherent developed a production unit dedicated to TMT at the company's plant in Richmond, California. A new machining center will perform Hex Cut operations on a total number of 231 polished roundels manufactured by Coherent.
During the kick-off review, Coherent laid out the schedule for the project and showed early small-scale models as the process development efforts
High Precision Lab Small-Scale Glass Model - Early small-scale development model to demonstrate the edge sensor pocket and precision glass cutting - Image credit: Coherent, Inc.
progress. The TMT team was particularly impressed with the Coherent team’s early efforts to mitigate risks using sub-scale models.
“The level of precision we are achieving is at the limits of modern manufacturing capability. The experience alone is a form of intellectual property and this is critical for achieving the quality, budget, and timeline requirements for the project,” said Greg Feller, Coherent Project Manager. “Coherent is incredibly proud to support the Thirty Meter Telescope and work side-by-side with the TMT team as they prepare for the telescope construction phase.”
More about TMT M1 Segments
At the heart of TMT is a revolutionary 30-meter diameter primary mirror composed of 492 hexagonal segments that work in concert, effectively as a single reflective glass surface. Each segment measures 1.44 m (4.7 feet) corner-to-corner and is 45 mm (about half the length of the long edge of a credit card) thick and weighs 0.25 metric tons (550 pounds). Prior to use in the telescope, each segment will be coated with a thin, reflective, multi-layered protected silver.
TMT’s hexagonal segmented array allows for an effective thirty-meter circular aperture. Further, the M1 mirror segments have a "high filling” factor and six-fold symmetry. The segments fit together with minimal gaps between them, maximizing the light capture. Each segment is separated from its neighbors by a 2.5-millimeter uniform inter-segment gap, preventing inadvertent contact and accommodating segment manufacturing, handling, and gravitational and thermal deformations of the mirror cell.
About Coherent, Inc.
Founded in 1966, Coherent Inc. is one of the world’s leading providers of lasers and laser-based technology for scientific, commercial and industrial customers. Our common stock is listed on the Nasdaq Global Select Market and is part of the Russell 1000 and Standard & Poor’s MidCap 400 Index. For more information about Coherent, visit the company's website at https://www.coherent.com for product and financial updates.
Approval of the first Production Roundel for Thirty Meter Telescope’s Primary Mirror
TMT Mirror Segment Shipping Container Design and Prototypes Completed through Collaborative Effort with Larson Packaging Company