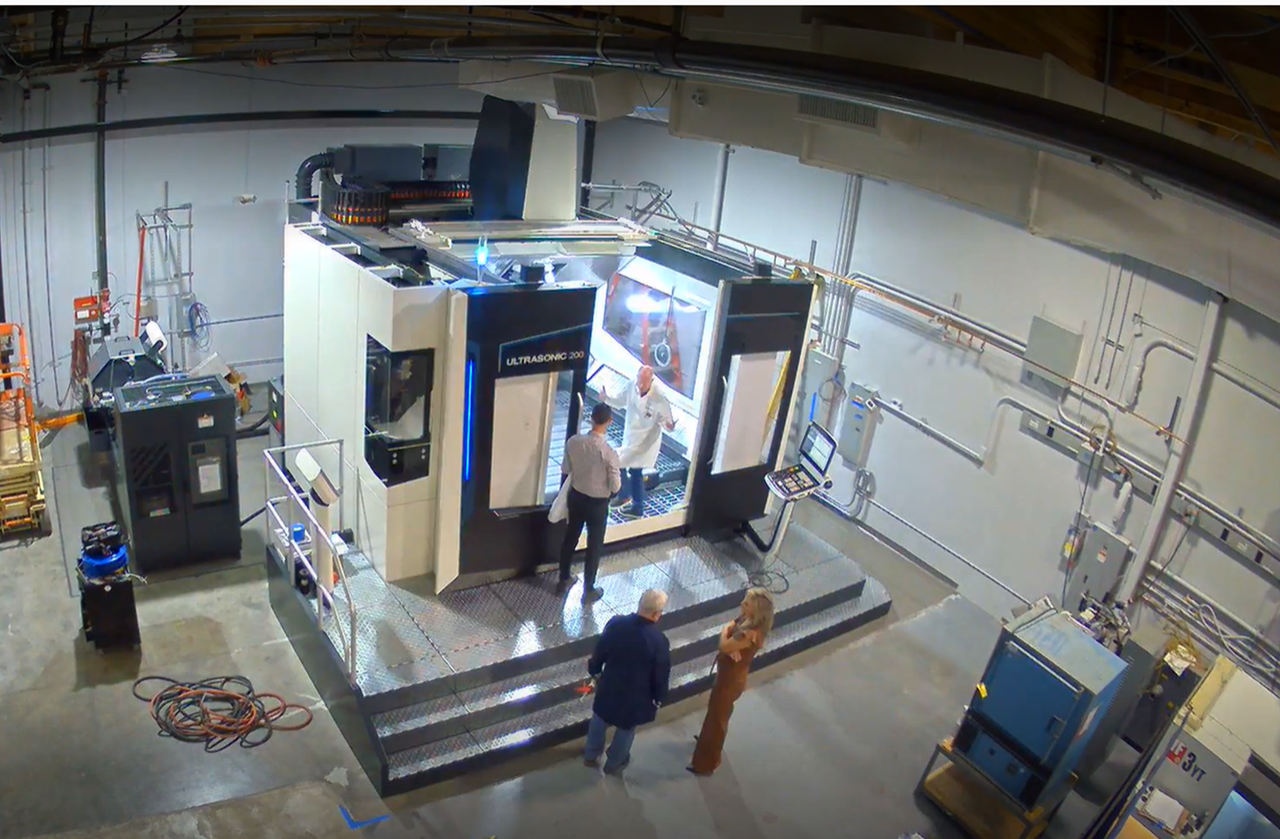
The Coherent ultrasonic-assisted machining system will be configured to handle precision hexing of the 230 TMT roundels currently being manufactured at Coherent facility in California. Image courtesy of Coherent Inc.
The Coherent ultrasonic-assisted machining system will be configured to handle precision hexing of the 230 TMT roundels currently being manufactured at Coherent facility in California. Image courtesy of Coherent Inc.
Coherent Corp., who is manufacturing all TMT roundels in the U.S., has expanded the optics facility dedicated to TMT. They have installed a new advanced ultrasonic machining tool designed to precisely cut the 230 roundels they produced for the TMT International Observatory.
As featured in the following news by Coherent, Coerent is completing the calibration procedure of this new tool and will start hexing TMT roundels in the coming months.
August 24, 2023 by Coherent
When it comes to telescope mirrors bigger is better. The fundamental physics of light dictates that as telescope aperture size increases, the images get brighter and more detailed. In theory.
In practice, as mirror size increases, it becomes harder to make them with a surface shape accurate enough to produce high image quality. The current practical limit on mirror size is about 8.5 m in diameter.
But scientists have developed a very clever workaround to avoid this limitation. Instead of making a single large telescope mirror, they now use a mosaic of smaller mirrors that act like a single, larger mirror. These individual segments are usually shaped as hexagons to allow them to be placed very close together.
Figure 1. Large telescope mirrors, such as the James Webb Space Telescope primary shown here, are often composed of numerous hexagonal segments placed close together (within 2 mm). Image courtesy of NASA Goddard Space Center.
This is precisely the approach being used to construct the Thirty Meter Telescope. This ground-based observatory is intended to deliver (infrared) images that are more than 12 times sharper than the Hubble Space Telescope, and four times sharper than JWST.
The Thirty Meter Telescope primary mirror will consist of 492 hexagonal segments, each of which is 1.44 m corner-to-corner. Coherent is fabricating 230 of these mirror segments.
These mirrors start with a 1.5 m diameter round shape. This is necessary because the “stress mirror polishing” technique we’re using to produce their off-axis, hyperbolic, freeform shape requires a rigid, symmetrical, round substrate. After the initial polishing process, these round mirrors (“roundels”) are shaped into hexagons (“hexing”).
Figure 2. Each of the 230 TMT roundels being fabricated by Coherent is 1.5 m in diameter and is subsequently “hexed” down to 1.44 m edge-to-edge.
This kind of shaping is common in optical fabrication and is typically performed with what is essentially a traditional milling machine, usually operated under computer numerical control (CNC). However, the various glass materials used for optics are very brittle and more difficult to machine than metal. Diamond tools are needed to work them.
Diamond machine tools have been in use for well over a century. They work great and are widely utilized throughout the optics industry. But even as modern automation enables them to work faster and more efficiently, they’re still relatively slow. This sometimes becomes an issue when removing large amounts of material from big optics.
Coherent (formerly Tinsley Optical Systems) engineers were confronted head-on with this limitation when tasked with hexing the 230 roundels we’re making for the TMT. We’d like to complete that program over the course of the next few years.
That probably sounds like plenty of time. It isn’t! If each roundel is hexed serially (one after the other on a single machine), it would normally take the better part of a decade to hex that many with a traditional milling system.
Over the past few years, tool builders have developed systems that incorporate an advanced form of ultrasonic machining. Specifically, this involves a small amplitude, rapid oscillation (in the tens of kHz range) of the diamond tool along its axis, in addition to the standard high-speed tool rotation.
This technology delivers several important benefits. First, it achieves a much higher material removal rate than traditional diamond tool milling – anywhere from 6 to 10 times faster. And, because the ultrasonic tool applies less force to the workpiece than a traditional tool, it typically produces little mechanical stress which avoids physical part distortion. This reduces sub-surface damage, yields a smoother finish, and enables production of thinner-walled features.
The lower force also reduces tool wear, which extends its lifetime. Plus, the ultrasonic tool is “self-dressing.” That is, fresh diamond grains automatically become exposed on the tool through use, which maintains its cutting power. Usually, tools must be periodically removed and dressed in a separate operation. Less frequent tool replacement and maintenance all reduces equipment downtime.
Manufacturers of large, high-precision parts – especially in the semiconductor industry – have adopted ultrasonic-assisted machining for just these reasons. But, to date, this technology hasn’t been employed for large optical components for aerospace and astronomy applications.
Coherent has become the first to do that by installing an ultrasonic-assisted machining system large enough to hex the TMT roundels. We’ve also developed some very specialized tooling for holding the optics within the machining center during the cutting process.
This tooling is critical because the 1.5 m diameter roundels weigh 0.25 metric tons (550 pounds) but are only 45 mm thick. So, it’s very easy to distort their shape by holding them in a way that applies any kind of asymmetrical or localized mechanical force. This can cause the part to “spring” when it is released from the fixture after cutting – changing shape enough that the machined features no longer meet specification.
It is therefore necessary to use “zero stress mounting.” Specifically, this is a mounting method that avoids distorting the roundel surface shape while still ensuring that the optic is held rigidly against the forces of the milling process.
A common approach when mounting optics for machining is to use a vacuum chuck. But there’s no way to achieve zero stress mounting of a freeform (asymmetric and aspherical) optic the size and precision of the TMT roundels with this method. It’s just not possible to make a mounting surface with a shape accurate enough to match the mirror.
Instead, Coherent engineers have created a proprietary tooling approach that employs a multi-technology network of support and clamping systems. These secure the part in all degrees of freedom without imparting any bending.
To maintain the cutting precision required for hexing the roundels, it’s also critical that the entire machining center rests on an extremely stable foundation. And the ambient environmental conditions must be kept constant, too. But, keep in mind, this machine tool is larger and heavier than a pickup truck.
As a result, we had to create a purpose-built facility to hold it. This started with pouring a new concrete mounting pad, extensively reinforced with rebar, to support the weight of the machine and provide the needed mechanical stability. Plus, we improved the temperature control within the entire production area to eliminate any changes in the ambient environment.
Read more about the roundel optical manufacturing process that precedes the hexing here.
TMT Monrovia Lab Visit
US Extremely Large Telescope Program Receives $15.3 Million from the National Science Foundation